
This is done with a “blind-stitch,” so-named because the needle penetrates only half the thickness of the material. The second step is sewing the seams so they hold together. The first step in this process involves gluing the suit’s neoprene panels with two or three coats of neoprene cement (hence the terms “double-glued” or “triple-glued”). The glued and blind-stitched seam tends to be found on colder water suits 3mm and thicker, primarily because this stitch doesn’t leak.

That’s why this style of stich is normally used on suits designed for warmer water where seepage isn’t such a critical factor. However, flatlock stitching does allow water to seep into the suit through its many needle holes. It’s also a flatter seam, hence the name, so it feels a lot more comfortable against bare skin. The flatlock stitch is easier and faster to make, so it tends to be less expensive than a blind stitch, and it allows more stretch to the seam, which can be helpful with today’s hyper flexible neoprene. This stitching method either butts or overlaps two pieces of material and then sews them together with multiple needles in a series of three or four rows of stitching, creating a very strong seam.
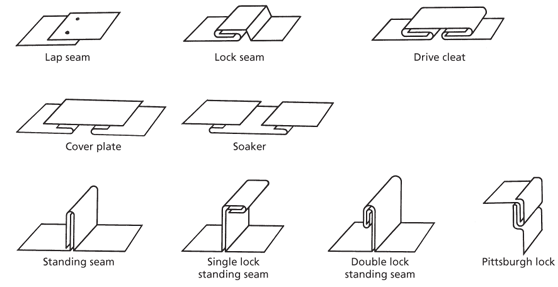
The flatlock stitch is commonly found in warm-water suits 3mm thick and less. There are basically two types of stitching being used in quality dive wetsuits these days: the flatlock (also known as flatseam) stitch, and the blind-stitch, which is used in conjunction with a gluing process. The type of stitching used to make these seams can make a huge difference in how comfortable and watertight a wetsuit will ultimately be. In wetsuit construction, seams are a critical component.
